Net Zero Case Study: Heartland Community College Agriculture Complex
Project Overview
Location: Normal, Ill.
Owner: Heartland Community College
Completion Date: 2024
Construction Type: New Construction
Building Type: Higher Education
Certification (being pursued): ILFI Zero Energy
Project Cost: $22 million
Project Team
Architect of Record: Legat Architects
Design Architect: Legat Architects
Engineering Lead: dbHMS
Civil/Landscape Engineer: TERRA Engineering
Structural Engineer: Nayyar and Nayyar
Commissioning Engineer: Baumann Consulting
General Contractor: River City Construction
Net Zero Rater: Living Building Challenge
Performance Data
Modeled Energy Use: Building 24.3 (Building + Greenhouse = 30.6)
Measured Energy Use: Verifying through Monitoring
Window to Wall Ratio: 25%
Gross Floor Area: 29,325 sq ft
Energy Modeling Software: Energy Plus – Open Studio
Energy Production: 19,215-square-foot solar panel array
Background
Heartland Community College in Normal, Ill. sought a new facility to anchor its agriculture education program and respond to central Illinois’ increasing demand for jobs in the industry. The administration wanted a facility that would not only enable the college to expand the program from 40 to 200 students, but also support new programming in precision agriculture, animal science, agronomy, regenerative agriculture, and more.
From the beginning, net zero certification was part of the discussions on planning the facility. For years before this process began, Heartland had been championing sustainability efforts across its campus. The college has a goal of achieving a net zero carbon footprint by 2050.
In its 2020 Master Plan, led by Legat Architects, the college affirmed its desire to develop a comprehensive energy reduction strategy, vowing to use it to further reduce its energy consumption and progress toward the development of more on-campus renewable energy systems.
At the project’s onset, the college expressed interest in net zero certification and asked the design team critical questions about funding and potential costs. After conducting research, Legat created budget ranges even before developing schematic design.
The team developed an OPR (Owner’s Project Requirements) document to identify key net zero goals for tracking the project’s progress. The building’s energy use target of 15 to 25 kBTU per square foot per year was set before design began.
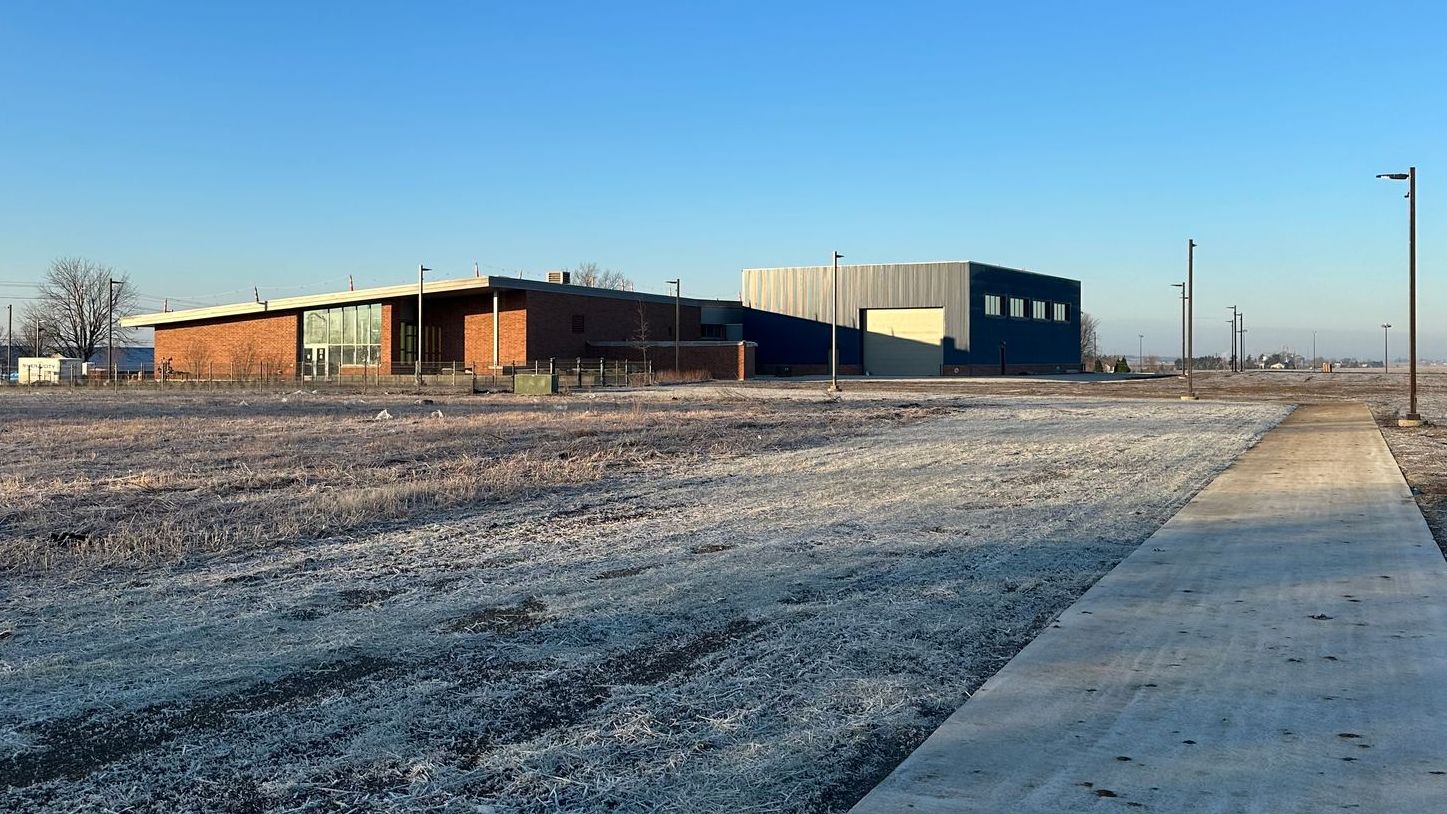
“If you want to go net zero, do your research, ask a lot of questions to others that have already built them, and consider the effort needed to maintain and monitor the systems,” Litwiller says. “The added material cost to achieve the proper envelope is something to consider, along with the additional costs in systems, monitoring, and maintenance.”
Sustainable
Strategies and Features
The design of the building stems from intensive energy modeling, passive solar principles, and solar compartmentalization, while the site design highlights stormwater management and flexible outdoor education.
One of the drivers behind this design was to create a teaching tool for students on net zero buildings. The team incorporated displays with real-time monitoring of the building’s energy generation and usage, informational signage about various aspects of the building, a floor cutout displaying what the radiant system looks like, and a display of the various layers used in the creation of the exterior walls of the building.
Renewable Power
The facility produces its own onsite renewable solar power. A nearly 20,000-square-foot rooftop array of south-facing solar panels is designed to produce over 354,700 kWh of power annually. Since the building was designed to only use 241,000 kWh annually, this means it is designed to produce more energy than it uses.
“Building the Agriculture Complex has given us the opportunity to familiarize our facilities staff with the operation of a solar array,” says Andy Litwiller, Executive Director of Facilities at Heartland Community College. “This will benefit us as we move towards the creation of a solar field north of campus.”
The campus itself features a wind turbine that began operating in 2012 and produced 64% of the total campus energy used in fiscal year 2024. A new ground-based solar array is currently in the design phase and is intended to pick up the remaining electrical demand on campus that is not covered by the wind turbine.
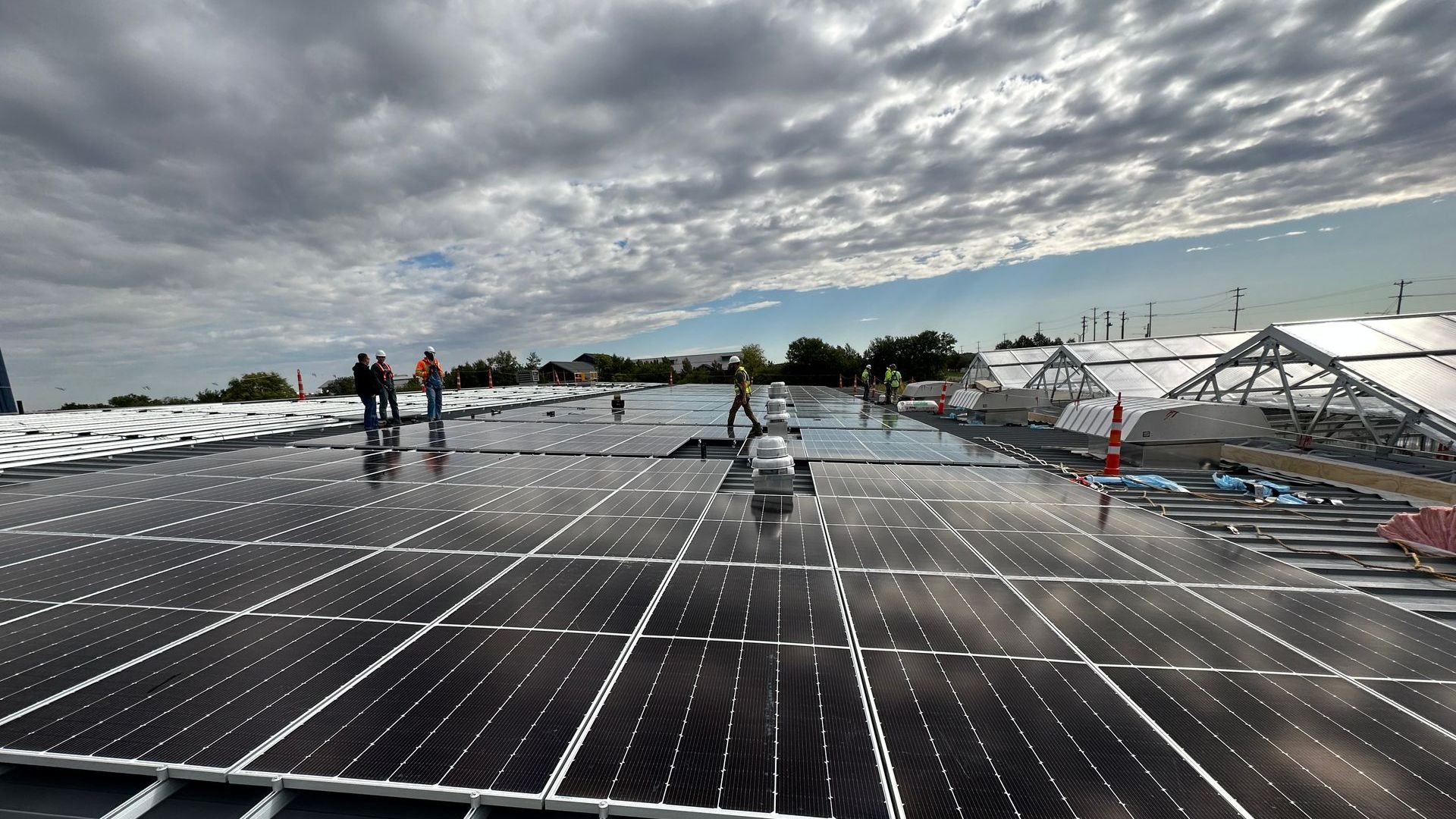
High Solid-to-Glazing Ratio
The percentage of solid (walls) to glazing (windows) is usually around 15-20% in most buildings’ facades. More than 25% of the Heartland Agriculture Complex’s facade is glazing, with optimized placement at strategic locations to give users both daylight and outdoor views.
Envelope Insulation
The building has a super-insulated envelope. In most buildings, walls are traditionally between eight and 14 inches thick from inside to out. In this building, however, the average wall thickness is over 26 inches. This extra density was achieved by layering more insulation into the building enclosure. The walls achieve an R40 rating, the roof has an R60 rating, the concrete floor has an R20 rating, and the windows are triple-pane glass with two layers of low-E coating.
High-Efficiency Mechanical System
The complex’s high-efficiency mechanical system features a ground source heat pump installed in the field northwest of the building to provide earth-cooled/warmed water to the building’s mechanical systems.
Lighting Systems
The team designed super-efficient lighting systems to further reduce energy use. High-efficiency programmable LED fixtures were selected to emit more light per watt than traditional fixtures, maintaining light levels while meeting a lower LPD (light power density) goal and saving energy and money without sacrificing performance.
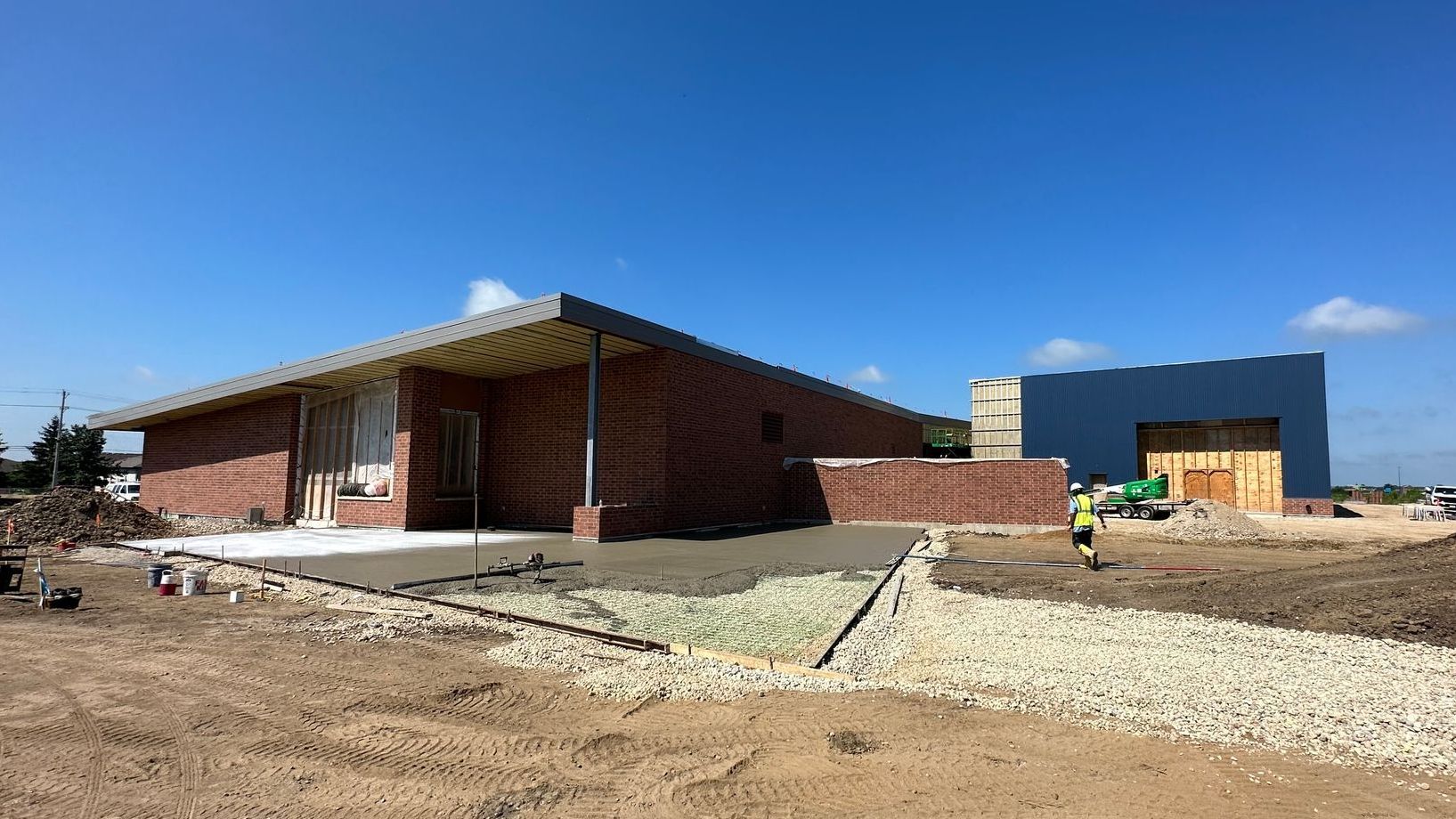
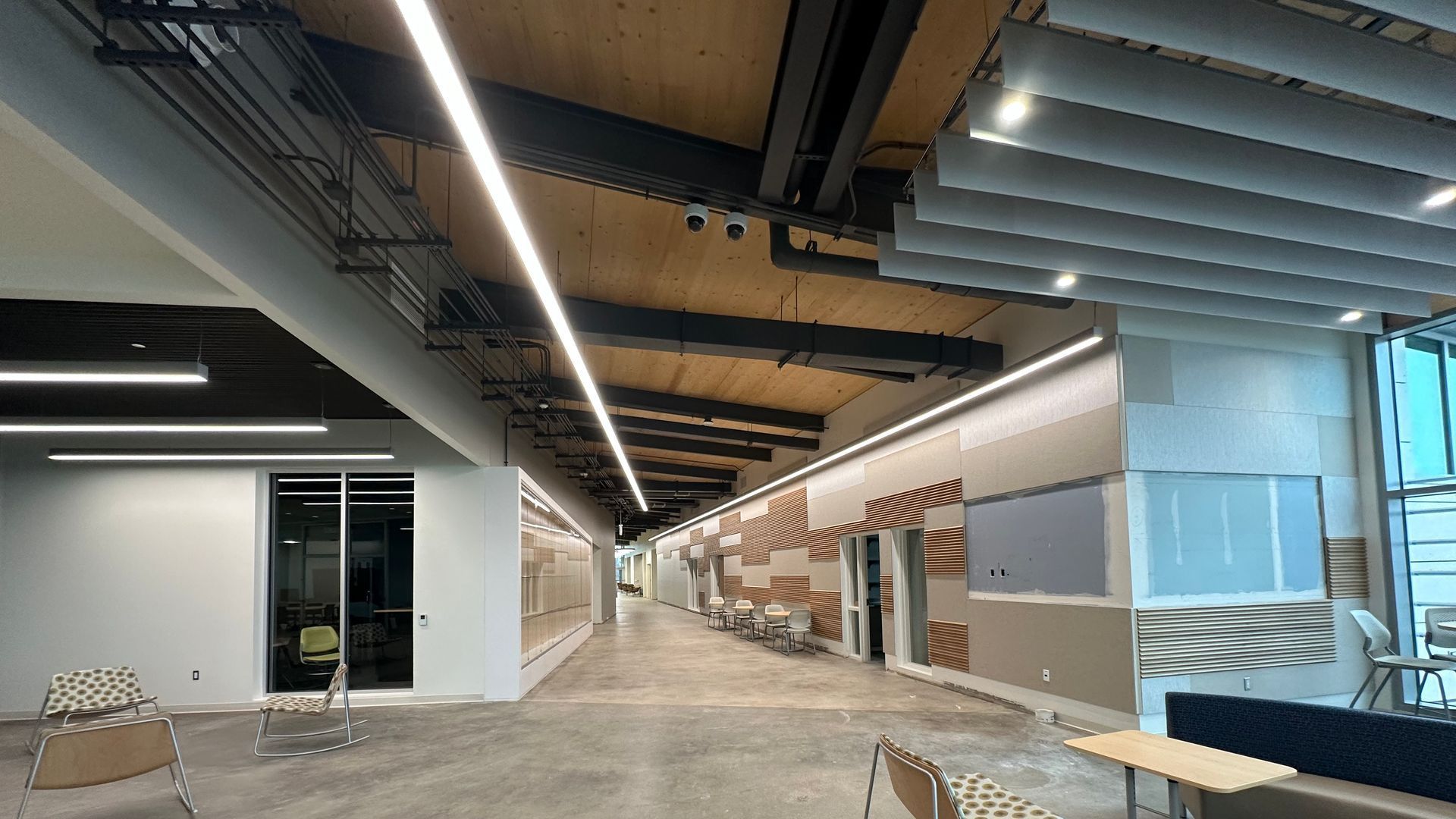
Financing
and Incentives
To help fund the work and materials related to the pursuit of net zero certification, Heartland applied for and received a $2 million grant from the Illinois Clean Energy Community Foundation. The grant supported the cost of the solar array, extensive energy modeling, superinsulation of the walls and roof, and the energy efficient geothermal radiant floor heating/cooling system.
Several donors also contributed to the cost of the building, with the rest of the project financed through bonds.
Given that the building is designed to supply all of its own energy needs, the college expects significant operating cost reductions to help offset the initial construction costs. In particular, the superinsulation and triple-glazed windows, as well as the geothermal system, should vastly reduce HVAC costs.

Heartland opted to go with the geothermal system at a higher initial investment because the equipment will have a longer overall lifespan, and because the administration and facilities team already has familiarity with geothermal since two of the college’s buildings are already powered by such systems.
Overcoming Challenges
Net zero projects require extensive testing, post-construction paperwork, and fine tuning to ensure that all building systems are functioning as designed and modeled. The Agriculture Complex officially opened in January 2024 but as of April 2025, has still not received net zero certification as the owners work through a series of issues related to the building systems.
One of the issues for the administration has been finding the right balance of heat pump HW/CW flow to dedicated outdoor air system (DOAS) units.
“The heat pump would trip out and fault out if it was too restricted on flow and finding the right speed to operate the valves and pumps throughout the system to meet demand in all areas proved to be a major hurdle,” Litwiller says.
Another challenge has been the underperformance of the solar array that is supposed to supply the building’s energy and a higher than anticipated energy demand from the greenhouse.
And given the complexities and more stringent requirements for net zero design and construction, there was more on-site education required for some members of the project team. Executing some of the finer details, mock-up, and testing was a challenge. To work around this, “we continually held meetings and reinforced the project requirements,” says Monique Taylor, Senior Interior Designer and Sustainability Coordinator at Legat Architects.
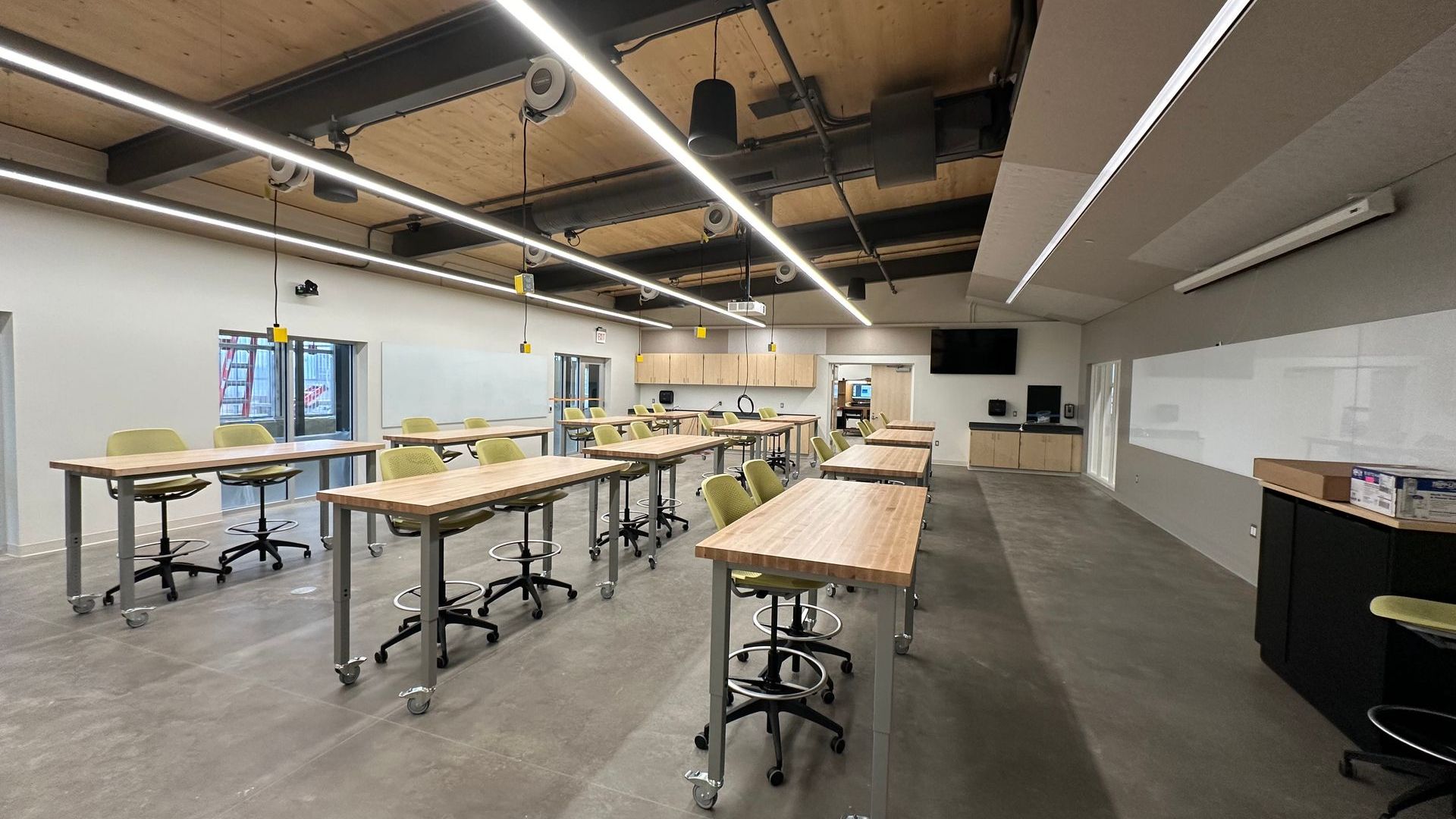
Lessons Learned
Simplify the Design
Based on their experience, the Heartland administration recommends keeping the design of a net zero project as simple as possible. “Overly complicated systems and controls add another layer to an already challenging building process and operation of the system,” Litwiller says.
Use an Integrated Approach
Legat notes that an integrated design approach is key to successfully completing a net zero project. Early collaboration among architects, engineers, contractors, and other stakeholders ensures that all aspects of the building work together to achieve sustainability goals.
Ensure Energy Modeling Accuracy
Another takeaway from this project is to ensure energy modeling accuracy. Accurate energy modeling is essential for predicting and optimizing a building’s performance. Real-world energy consumption can vary from initial models, so ongoing monitoring and adjustments are necessary for optimal results.

“The team should not rely on just one energy model for accuracy,” Taylor says. “The commissioning agent and the mechanical engineer should both build energy models, and they should verify the alignment of the models during the design process.”
Educate Occupants on Energy Use
Occupant behavior can have a significant influence on a building’s energy use. Educating occupants about energy-efficient practices and providing user-friendly control systems can improve the building’s overall performance. At the Heartland Agriculture Complex, the team showed the users of their greenhouse how to operate temperature and light controls.
The architecture/engineering team designed a building user manual intended to be distributed to occupants to provide simplified usage and maintenance information for regular building users/occupants. It includes room set points, cheat sheets for maintenance personnel, and pictures of controls in each section of the building with explanations of how to use them.
Prioritize Operations and Maintenance
Regular maintenance and proper operation are critical for sustaining net zero performance. Building operators should be well-trained, and maintenance plans should be in place to address any issues promptly.